Integrators are faced with a fast-moving picture when it comes to choosing the correct interface for their vision system, finds Tim Gillett
The giant steps taken in industry 4.0 have led to fast-growing opportunities in the industrial vision marketplace in recent years, with inspection and security products seeing wide commercialisation, particularly in the manufacturing sector.
Fast growth in smart manufacturing technologies worldwide have led to an increased demand for vision systems that are able to provide quality control automation and inspection. This trend has fired growth through the overall industrial vision sector; the global industrial camera market was valued at $12.9bn in 2021 but is predicted to grow at more than five per cent for the next decade with an estimated worldwide value of $21.5bn by 2031.
According to a survey on the industrial vision market in June this year, by Transparency Market Research: ‘A rise in need to monitor the harsh environmental conditions to prevent accidents in industries such as mining is augmenting the demand for industrial security cameras, industrial CCTV cameras, and industrial inspection cameras.
‘Additionally, the advent of Industry 4.0 has resulted in rapid changes in the manufacturing sector, with the development of new and augmented networking systems across the world. This opens up lucrative opportunities for industrial camera manufacturers to introduce highly enhanced industrial camera systems for end-use applications.’
Drivers – more complex equipment, more varied markets
With the general growth of the vision industry, and its widespread use in ever-more diverse applications, comes an increased focus on the plethora of interfaces used to connect cameras and the wider systems in which they are used.
The last few decades have seen the development of various different interfaces, guided by scientists and industrial groups to define, maintain and standardise them. Users of vision systems have also been tasked with keeping on top of the relevant information regarding the capabilities of each interface to ensure they have made the correct decisions when procuring
industrial vision equipment – no easy task given the rapid development in the marketplace and the constant rise in the number of new applications for vision systems.
While industrial and scientific cameras have moved on impressively in terms of speed, quality and improved sensor design, the use of the right connectors and cables into vision systems continues to augment and push the boundaries of imaging applications with higher bandwidths and more reliable data transfer.
Different requirements
According to Eric Bourbonnais, software designer at Teledyne Dalsa and chairman of the GigE Vision Committee at the Automated Imaging Association, for users – and, specifically, for buyers at industry integration companies – the key aspect to understand is that there are a plethora of complex options when it comes to interfaces, and that the choices made are very much dependent on the requirements of the job in hand.
He added: ‘Of course, it needs to be considered that camera technology is moving fast – not just at the front end with sensor design, but within the camera interfaces themselves. Ethernet capabilities are growing fast too, and CPU advances mean there are new and faster ways of managing data and leveraging an internet that is improving constantly in terms of speed and reliability.
‘We, and the wider industry, are bringing new connectors and cables into vision systems and this is helping to push the boundaries of imaging applications with higher bandwidths and more reliable data transfer. It is important for the industry to leverage and improve what has already been developed, by developing standard equipment and evolving systems that are already in place.’’
Key interfaces
The simplest interface – largely due to its ubiquity and its long history – is the universal serial bus, commonly known as the USB. The interface has been in use for more than 25 years and, to this day, most personal computers come equipped with at least two USB3 ports as standard. Obtaining or replacing USB parts is easy and cheap, and the interface has very few compatibility issues, meaning that a large number of USB cameras can be added to a vision system without prohibitive costs.
Following in the footsteps of USB, and introduced around a decade later, came GigE Vision – aimed at high-performance industrial cameras and allowing the transmission of high-speed video and related data via Ethernet. The GigE standard was introduced by a group of 12 vision companies, and is administered by the Automated Imaging Association. A key benefit of GigE Vision is that it allows multiple cameras to be controlled and synchronised on a 24-hour basis from a remote location. The most powerful GigE cameras, 5GigE, are capable of speeds up to Gb/s, while a TurboDrive system from Teledyne Dalsa can potentially further double the standard data rate.
The CoaXPress (CXP) interface, as the name suggests, uses coax cables that require being attached to a frame grabber, or capture card. This system allows a higher performance and the capability to process larger amounts of data and increase a given system’s overall bandwidth with maximum speeds of 25Gb/s using cables of up to 35m in length.
CameraLink, developed around 20 years ago, is designed to be an easy and reliable way to connect cameras and frame grabbers. Using this system, cables of up to 10 metres can be used, though this needs to be reduced slightly when running at full capacity. Speeds of up to 850MB/s are achievable and multiple cameras can be controlled through one interface.
CameraLinkHS (CLHS), developed around 10 years ago, uses standard cables or fibre optics to maximise speed and range. CLHS can connect over distances as long as 5,000m when using fibre cabling, with speeds of more than 50 Gb/s on a single cable.
Conclusion
The vision industry appears set to continue its fast growth in the coming years, with smart manufacturing technologies requiring the implementation of systems for quality control automation and inspection across a huge range of widely-differing applications.
Clearly there is a wide variety of camera interfaces available, and a decision as to which one best suits a particular imaging application can be a difficult one given the multitude of variables in play. These include the distances involved and therefore the length of cable required, the speed of data transfer required, and of course the cost implications for the buyer both in terms of the original set-up and the ongoing need to maintain, improve and develop the system in question.
Bourbonnais concluded: ‘Buyers at integration companies need to understand the bandwidth, synchronisation, ease of deployment, and cable length that each interface offers, and then it becomes much easier to make a decision. By comparing the bandwidth of each interface, the difference in how much image data can be collected becomes clear.
‘Using a CXP or CLHS camera will provide much higher bandwidth for a vision system, but in applications where a frame grabber is not necessary or not possible, options such as USB and GigE become a good choice. Deciding which interface best suits a particular system comes down to the needs of the application.’
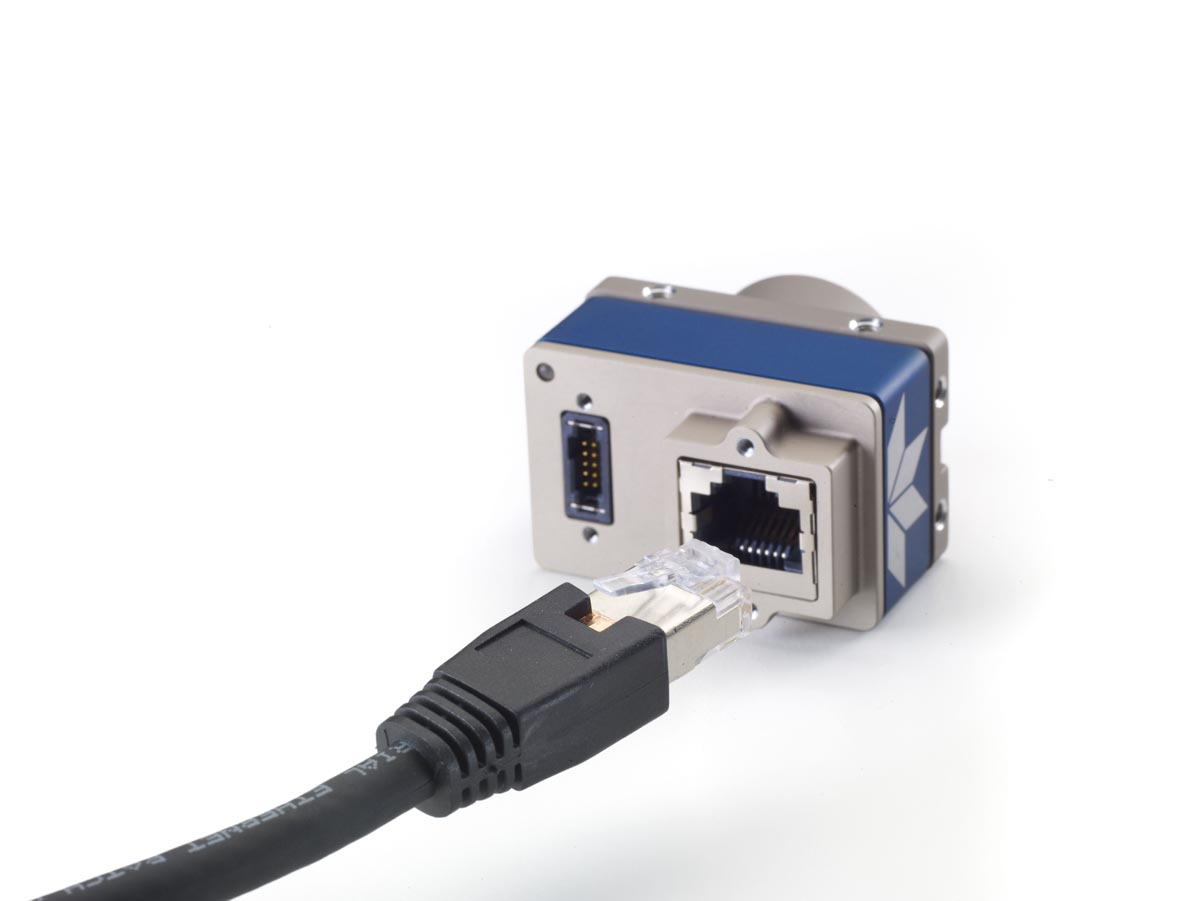
There are many types of cables and connectors used with today’s industrial cameras. To gain a greater understanding of the available interfaces within the industrial and scientific area scan camera market, download the latest white paper.