Breaking the boundaries of smart camera and embedded vision systems
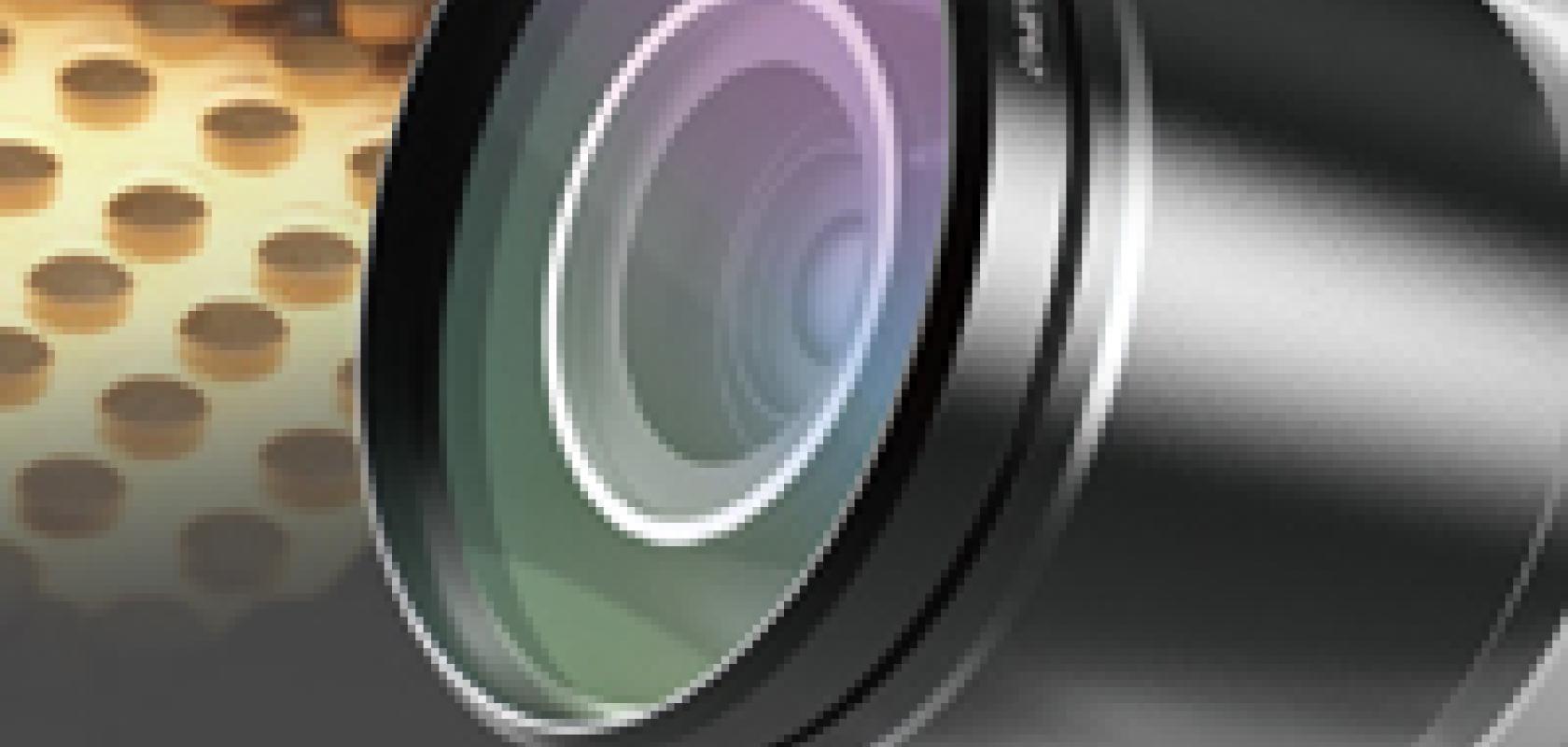
Types of vision system
Smart cameras are small, compact, all-in-one vision systems that incorporate lens, image sensors, system storage and processors into a single device combining camera and computer.
Theoretically, more powerful processors are capable of executing more complex tasks at higher speeds. However, they also draw more power and require larger physical size to accommodate heat dissipation measures. A fan, for instance, can be a disadvantage in rugged environments, as moving parts can easily fail.
Consequently, smart cameras have generally made use of a low power ARM-based or single-core Intel® Atom™ processor with limited memory, in consideration of size and ruggedness. The minimal memory capacity available limits the ability to process high-resolution images with sufficient speed for most industrial processes, as well as impedes multitasking.
Accordingly, conventional smart cameras are often single-purpose, dedicated to simpler image tasking-such as gauging, counting, alignment, or barcode scanning. Due to their minimal expandability, implementing additional functions requires installation of more system units.
When more complex, high performance machine vision applications are to be undertaken, and expandability is demanded, users often turn to the second category of vision system: embedded vision systems. These systems include an industrial PC connected to one or more high-resolution industrial cameras. The industrial PC typically features a high-performance processor running a standard PC operating system with multiple vision channels supported, to deliver a full set of image processing functions. Rich and versatile I/O connectivity allows flexible connection with other field devices in the factory.
Embedded vision systems are, however, often more costly and complicated to deploy. The increased footprint compared with smart cameras is also disadvantageous in space-constrained production floors. More cables and possible need for fans also affect system reliability.
Intel’s introduction, in the 4th quarter of 2013, of the high performance, low power consumption Intel® Atom™ processor E3840 has ushered in a new category of vision system. These systems are small and compact all-in-one systems with full PC functionality, high resolution, high frame rate, and solid multitasking performance. In addition, they offer flexible expandability and easy deployment.
We call this the new generation of machine vision x86 smart camera because, it enables highly integrated and high performance small vision systems based on Intel® processors, a new market trend this paper addresses.
Smart factory requirements
- High efficiency and throughput
System efficiency and throughput is critical for the higher productivity most industrial manufacturers pursue. However, there is a cost. In terms of conventional machine vision system, high resolution and high frame rate are hard to achieve at the same time.
In reality, vision applications are often a marriage of high resolution with lower frame rate, or lower resolution with higher frame rate. To achieve both, a more advanced CPU is needed with costs raised commensurately. Striking the delicate balance necessary among these factors and achieving optimal efficiency with reasonable cost structure is an important issue faced by system developers on an ongoing basis.
- Ruggedness and reliability
Industrial operating environments are often challenging for automated systems in different ways. For example, a food and beverage production facility is likely to present damp conditions with extreme temperatures, while machine tooling environments are often dusty with metal or other intrusive particulates present. If the vision system is to be installed adjacent to production equipment, a high degree of imperviousness to a range of elements is needed.
- Integration with 3rd party equipment
A production line usually involves a series of operations – manufacturing, machining, pick and place, inspection, packaging, and more. For instance, in CNC turning operations, a number of different machines are used with an external controller, such as conveyors or robotic arm, to move components from machine to machine and align them under the guidance of industrial cameras before cutting operations commence. After turning, the objects are conveyed to the next operation stand for flaw inspection. Finally, approved products are sent to packaging and undergo barcode reading for shipping. Integration of and communication among the different systems involved is a challenge for all smart factories.
- Faster development
Development of software solutions and related compatibility issues are critical factors, often dictating the success or failure of the implementation. Shortening development time and reducing system development costs present distinct challenges.
Implementation Factors to Consider
- CPU efficiency
As mentioned, conventional smart cameras usually run on a single-core Intel Atom processor or ARM-based processor to meet requirements in size, power and heat dissipation. However, these conventional smart cameras have limited computing power and are often used only in simple image applications dealing with individual tasking of gauging, counting, alignment, or barcode scanning.
The Intel Atom processor E3840 provides twice the performance over the previous generation processor while keeping power consumption under 10 W, enabling multitasking in a fanless small system.
Multitasking systems can reduce the number of installations, an economic advantage in terms of total cost of ownership (TCO).
- Image sensors
Image sensors are the eyes of vision systems. Larger sensors can acquire more image information and deliver higher image quality. In the past, with conventional smart cameras focused on simple imaging tasks, the size of image sensors was not an issue. However, with the implementation of high-end and high-speed applications, image sensor size becomes critical for image quality.
- Rolling shutter vs. global shutter
Rolling shutters and global shutters differ in the way their pixels collect light. Rolling shutters collect light in sequential rows, with each row starting and finishing collection slightly different from each other. Global shuttering pixels start and end light collection during exactly the same period of time.
Conventional smart cameras, because their limited computing power is insufficient to process large amounts of image data, have tended to adopt the rolling shutter. However, the inability of rolling shutters to remove residual signals when dealing with fast-moving objects (with attendant blur/skew/blur/ skew/wobble/partial exposure effects), has excluded conventional smart cameras from use in high-speed industrial applications. Currently, with the improved CPU efficiency of the new generation Intel Atom processors, small form factor smart cameras are able to support global shutter deployment.
- Coprocessor
While image quality is critical for accurate automatic inspection and analysis, limits in optical conditions (light source or lens) frequently cause acquired images to exhibit inconsistent brightness, leading to misjudgment in analysis. If the vision system can automatically optimize acquired images before submission for analysis, accuracy of image analysis is significantly enhanced.
In conventional vision systems, captured image data is processed by the CPU. When processor resources are insufficient, the amount of image data able to be processed is reduced. Thus, conventional smart cameras must frequently compromise either image resolution or frame rate.
The use of an FPGA coprocessor by the new generation x86 smart cameras greatly improves image processing efficiency by offloading image matrix operations from the CPU to the FPGA (image preprocessing), freeing CPU resources to carry out more advanced algorithmic operations. The FPGA coprocessor can carry out image preprocessing tasks such as LUT (look up table), ROI (region of interest) and shading correction, with smaller vision systems accordingly realizing faster and more complex applications.
- Graphics and Media Processing
The new generation Intel Atom processor E3840 adopts a GPU driver which offloads media processing tasks from the CPU and triples graphic processing performance over the previous generation processor. Using the integrated Intel® 7th Generation HD Graphics technology, the GPU can process video encoding, compression and transmission across multiple channels simultaneously. This performance improvement empowers small vision systems to record, store and analyze media data, resulting in a “smarter” factory.
- Display
Conventional smart cameras transmit data via only an Ethernet cable connected to the control center. If the vision system can also connect with HMI or a screen at the production line via VGA or Ethernet port and display image data simultaneously, operators can view inspection results and find problems earlier.
- 64-bit computing
As image analysis applications are required to manage large amounts of data, most mainstream software tools in this segment utilize 64-bit instructions. It is incumbent, therefore, to deploy a vision system that supports 64-bit computing.
- System storage
System storage capacity can determine whether the vision system is able to run a full PC OS and 3rd party APIs, in addition to the amount of image samples the system can store for matching and comparison.
- Total cost of ownership (TCO)
Total cost of ownership is not determined solely by the nominal price tag of the system, but rather a combination of factors, including space usage, peripheral support, system expandability, and software development costs.
A. Space usage: The physical size of the vision system including external cabling should be considered as a production space cost. External wiring and cabling as well as extended peripherals such as PWM light source controllers must also be taken into account.
B. System expansion cost: The number of channels the vision system provides define its expandability. Conventional smart cameras, though cheaper in single unit price, present the need for more system units to accomplish necessary expansion. This makes actual system costs are much higher. The new generation x86 smart camera systems provide multiple channels and a GigE port supporting an additional slave camera, obviating the requirement to install additional system units to add a function and reducing average channel expansion costs.
C. Software development and versatility: As mentioned, a manufacturing facility comprises multiple operation stands, among which effective communication and integration determines actual factory efficiency. If existing software resources can easily migrate across systems, human resource and development costs in deployment are dramatically reduced.
Winning strategies of the new generation x86 smart camera
- Small system delivering high performance and efficiency
New generation x86 smart cameras running on the quad-core Intel Atom processor E3845 deliver serious improvements on CPU and GPU performance while conserving power expenditure. The new processors provide the palm-sized x86 smart cameras with the combined advantages of both conventional smart cameras and embedded vision systems.
- Coordination among CPU, GPU and FPGA co-processor
The FPGA coprocessor and integrated GPU of the Intel Atom processor E3845 help offload tasks from the CPU, releasing resources for more advanced computing. Multitasking is thus viable, allowing the x86 smart camera, though small in form factor, to simultaneously manage gauging, counting, alignment, and 2D barcode reading operations.
- Have it both ways
In the past, with conventional smart cameras, high speed, high resolution, complex image processing was unattainable at the same time. The new generation high-efficiency quad-core Intel Atom processor E3845 in the x86 smart camera easily support 4MP 60fps global shutter sensors and high-speed inspection, while implementing complex image analytics with the help of the FPGA coprocessor and 64-bit compatibility.
- High flexibility and reliability
New generation x86 smart camera systems can provide an I/O topology similar to those in embedded vision, including GigE, VGA, RS-232, USB ports and isolated DI/O, maximizing communication and integration with other devices on the production line. IP-67 rated housing provides secure protection from moisture, dust, and other contaminants, delivering operational reliability in harsh industrial environments.
- Open software architecture reduces total cost of development
The new x86 smart camera provides compatibility with GeniCam and GenTL standards for image acquisition, as well as an intermediate platform with the same API to communicate with 3rd party software. With versatile open architecture, programs written by developers can easily migrate to different devices, shortening software development time and reducing total cost of system expansion.
ADLINK x86 smart camera solution
ADLINK’s NEON-1040/1020 is the industry’s first quad core x86 smart camera that realizes advantages of both conventional smart cameras and embedded vision systems in a compact palm-size housing of 68.5W x 110L x 52.7H mm.
Featuring the 1.91 GHz quad-core Intel Atom processor E3845 , high-end global shutter, FPGA support, 64-bit instruction, onboard 2 GB RAM and up to 32 GB system storage, the NEON-1040/1020 can implement high-speed and complex industrial applications with a minimal footprint.
The image preprocessing functions provided by the FPGA coprocessor include LUT (look up table), ROI (region of interest) and shading correction, helping to reduce CPU loading and enable complex acquisition at high speeds.
ADLINK’s x86 smart camera, the NEON-1040/1020, adopts an open software development architecture providing flexible support including GeniCAM, GenTL support for image acquisition, and Open CV and Open CL programming. System integrators only need learn a programming language and use this intermediate platform for easy migration. This helps to simplify integration with motion, I/O, and other devices; speed deployment; and reduce total cost for system expansion.
Rugged, sturdy, washable IP67-rated casing and M12 connectors come together to allow the NEON-1040/1020 to withstand the harshest industrial environments, such as machine tooling and food/beverage processing applications.
Peripheral support includes an additional GigE port to connect with external devices, such as GigE Vision slave cameras, and EtherCAT with I/O control modules. The built-in PWM lighting control conserves TCO while communicating with LED lighting.
Versatile I/O support includes 4 x digital inputs, 4 x digital outputs, USB 2.0 port, RS-232 ports, and VGA output, maximizing convenience for factory automation users.
Conclusion
For modern mass production processes, the implementation of automated inspection is crucial in ensuring manufacturing quality and productivity, a primary requirement in enhancement of corporate competiveness.
Time and money are always key factors defining competiveness, and it is important for system implementers to choose a system that effectively minimizes cost and time to market.
The x86 smart camera defines a new category of vision system that singularly realizes high-performance, maximum integration, easy deployment, space efficiency and minimal total cost of ownership – all well beyond what conventional systems can achieve.
About ADLINK
ADLINK Technology is enabling the Internet of Things (IoT) with innovative embedded computing solutions for edge devices, intelligent gateways and cloud services. ADLINK’s products are application-ready for industrial automation, communications, medical, defense, transportation, and infotainment industries. Our product range includes motherboards, blades, chassis, modules, and systems based on industry standard form factors, as well as an extensive line of test & measurement products and smart touch computers, displays and handhelds that support the global transition to always connected systems. Many products are Extreme Rugged™, supporting extended temperature ranges, shock and vibration.
ADLINK is a Premier Member of the Intel® Internet of Things Solutions Alliance and is active in several standards organizations, including PCI Industrial Computer Manufacturers Group (PICMG), PXI Systems Alliance (PXISA), and Standardization Group for Embedded Technologies (SGeT).
ADLINK is a global company with headquarters in Taiwan and manufacturing in Taiwan and China; R&D and integration in Taiwan, China, the US, and Germany; and an extensive network of worldwide sales and support offices. ADLINK is ISO-9001, ISO-14001, ISO-13485 and TL9000 certified and is publicly traded on the TAIEX Taiwan Stock Exchange (stock code: 6166).
About the Intel® Internet of Things Solutions Alliance
From modular components to market-ready systems, Intel and the 250+ global member companies of the Intel® Internet of Things Solutions Alliance provide scalable, interoperable solutions that accelerate deployment of intelligent devices and end-to-end analytics. Close collaboration with Intel and each other enables Alliance members to innovate with the latest technologies, helping developers deliver first-in-market solutions.