Understanding machine vision verification of 1D and 2D barcodes
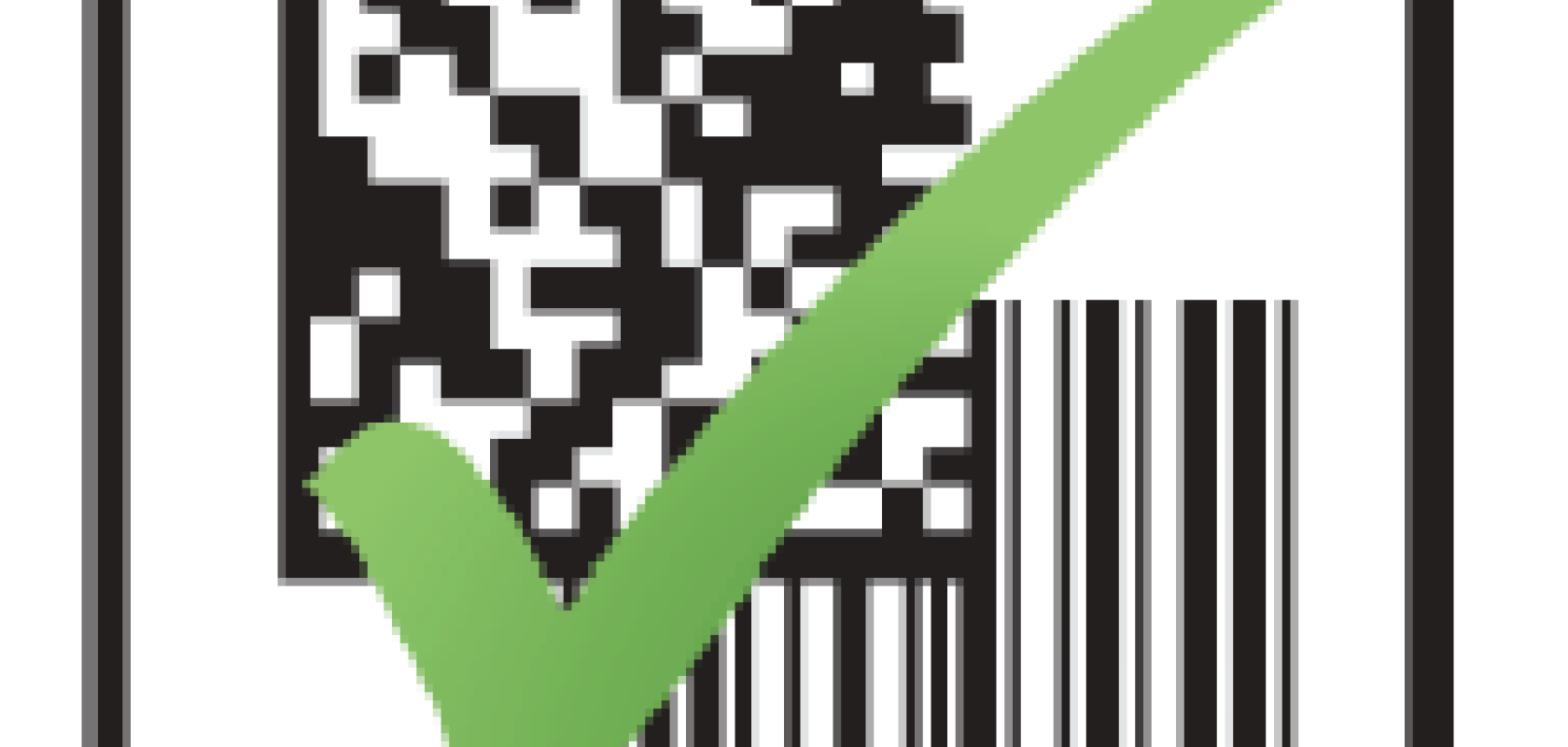
Legible, accurate barcodes have never been more important than they are today, when automated supply chains depend on data accuracy to ensure the reliable performance of global operations. Machine vision verification is one tool that can be used to ensure that barcodes meet a consistent level of quality for readability in an automated process, and that bad codes are identified before they result in costly failures. This white paper introduces 1D and 2D barcode verification and identifies parameters for verifying codes against published standards.
Why verify?
Barcode quality is integral to the success of an automated system. In a process where quality barcodes accurately store and communicate data – from code to reader to central system – little manual intervention is required. Thanks to quality barcodes, the unique benefits of an automated system are realized: lower costs, higher productivity, and fewer errors. Poor quality barcodes, however, render the system almost as inefficient as using no automation at all. Unreadable barcodes may require re-labeling, re-scanning, or even manual entry of critical information by a human operator – disrupting the productivity of the process and causing a significant loss of time. Bad barcodes may prevent error-tracking, causing a domino effect of failures down the line and resulting in costly scrap and rework. All told, these effects completely counteract the benefits of implementing an automated system, the result being inflated cost, loss of productivity, and increased errors.
The purpose of barcode verification is to prevent this outcome and preserve the intended benefits of the automated system. Verification systems evaluate a barcode’s quality against published quality standards for 1D and 2D barcodes using precision instruments such as barcode verifiers or machine vision systems. A verified barcode ensures consistent readability, supporting 100% accurate automated data capture.
When should you verify?
To ensure that errors are prevented as early in the automated system as possible, verification must occur before a part enters the system. A verification step should occur after a part is marked or labeled with a barcode and before the the part reaches the station where the barcode is first read.
Proper verification ensures that every part is processed and shipped with a high-quality barcode, despite the fact that marking and labeling systems will degrade over time. A verification system is much more accurate than a standard barcode reader at identifying low-quality barcodes early in the process, before parts with bad barcodes make it through the line and are shipped to end customers. When barcode quality degradation is identified early, the marking or labeling system may be adjusted or replaced before unreadable barcodes are ever produced.
Without verification, bad barcodes are not identified until they are unreadable. By the time a bad barcode is identified, several poor-quality barcodes may have already escaped down the line.
With verification, bad barcodes are prevented from being applied to the product, eliminating the chance for future failures.
Validation vs verification
Depending on the requirements of a particular process, industry, company, or customer, there are two levels of quality grading for ensuring barcode readability: validation (sometimes called process control) and true verification.
Validation/Process Control: Process control is a means of ensuring that barcodes are readable throughout a particular internal or internal/external process. Process control does not check barcodes for compliance to a published barcode quality standard. Instead, it provides objective measurements for barcode quality when verification to a standard is not possible or not desired. If you are not concerned with meeting published barcode quality standards in your application, you may opt to use a subset of the default verification parameters in the verification system as the criteria for passing codes.
Verification: Verification ensures that a barcode complies with published barcode quality standards, such as ISO 15415, ISO 15416, and AIM DPM. To ensure compliance, all evaluation parameters in the machine vision system must be enabled during the verification process. Fully-conforming verification systems provide reports as evidence of barcode compliance, which can be sent to customers or other invested parties to provide the highest assurance of barcode quality and consistency.
What kind of hardware is required?
More precise quality grading requires higher-performance hardware. If a symbol must meet parameters for internal/external process control only, a machine vision system with integrated lighting may be adequate for performing validation. However, barcodes that must comply with published barcode quality standards must be verified by a system with superior optics, such as a C-mount lens, and with complete and uniform lighting by an ISO/AIM-compliant light to produce an undistorted image.
Verification evaluation parameters
There are a number of verification evaluation parameters that determine barcode quality and they may be used for either true verification or validation/process control. Published barcode quality standards, such as ISO 15415, ISO 15416, and AIM DPM, require that a designated set of these parameters be met to ensure that a barcode is verified to the standard, while process control grading may require that a barcode meet only a subset of these parameters. Parameters for 1D and 2D barcode evaluation are shown below.
Verification grades
Barcodes are graded by verification equipment like barcode verifiers and machine vision systems, which assign values 0-4/A-F to the barcode for each of the above-listed evaluation parameters. A barcode’s overall grade is determined by the worst result for each parameter, so the barcode is always as good as its poorest parameter. Typically, a barcode with a grade A, B, or C is considered acceptable quality, while a grade D or F signifies a poorly marked or poorly-printed barcode.
Verification with AutoVision
Microscan’s AutoVISION Machine Vision Software provides powerful tools for both text quality verification (OCV or Optical Character Verification) and barcode quality verification.
Using AutoVISION and high-performance smart cameras and lighting, you can set up a complete verification system to determine barcode quality at any level of quality grading, including conformance to three published barcode quality standards:
ISO 15415 AIM DPM ISO 15416
Clear and concise values are provided via the AutoVISION user interface to grade 1D and 2D barcodes for each parameter required by a particular barcode quality standard. AutoVISION assigns values 0-4/A-F to the barcode for each parameter and then the barcode receives an overall grade for meeting the quality standard.
Default parameters in AutoVISION are pre-set to grade barcodes against published barcode quality standards (ISO 15415, ISO 15416, and AIM DPM), but can be adjusted in the AutoVISION Symbol Quality Verification Tool to enable process control grading for barcodes that must meet application-specific criteria only.
Microscan Meets Verification Needs
From 2D barcode verifiers to complete, scalable machine vision systems like AutoVISION, Microscan offers a range of products to ensure that automation systems operate at peak performance thanks to quality and compliant barcodes. For engineers tasked with meeting quality control or global standards in marking and labeling, Microscan provides project evaluations to find the right barcode verification solution for any project.
More Microscan product information and training resources are available at www.microscan.com.
Verification evaluation parameters are adjusted in the AutoVISION Symbol Quality Verification Tool to grade a barcode for internal process control.