Best Practices For Better Imaging
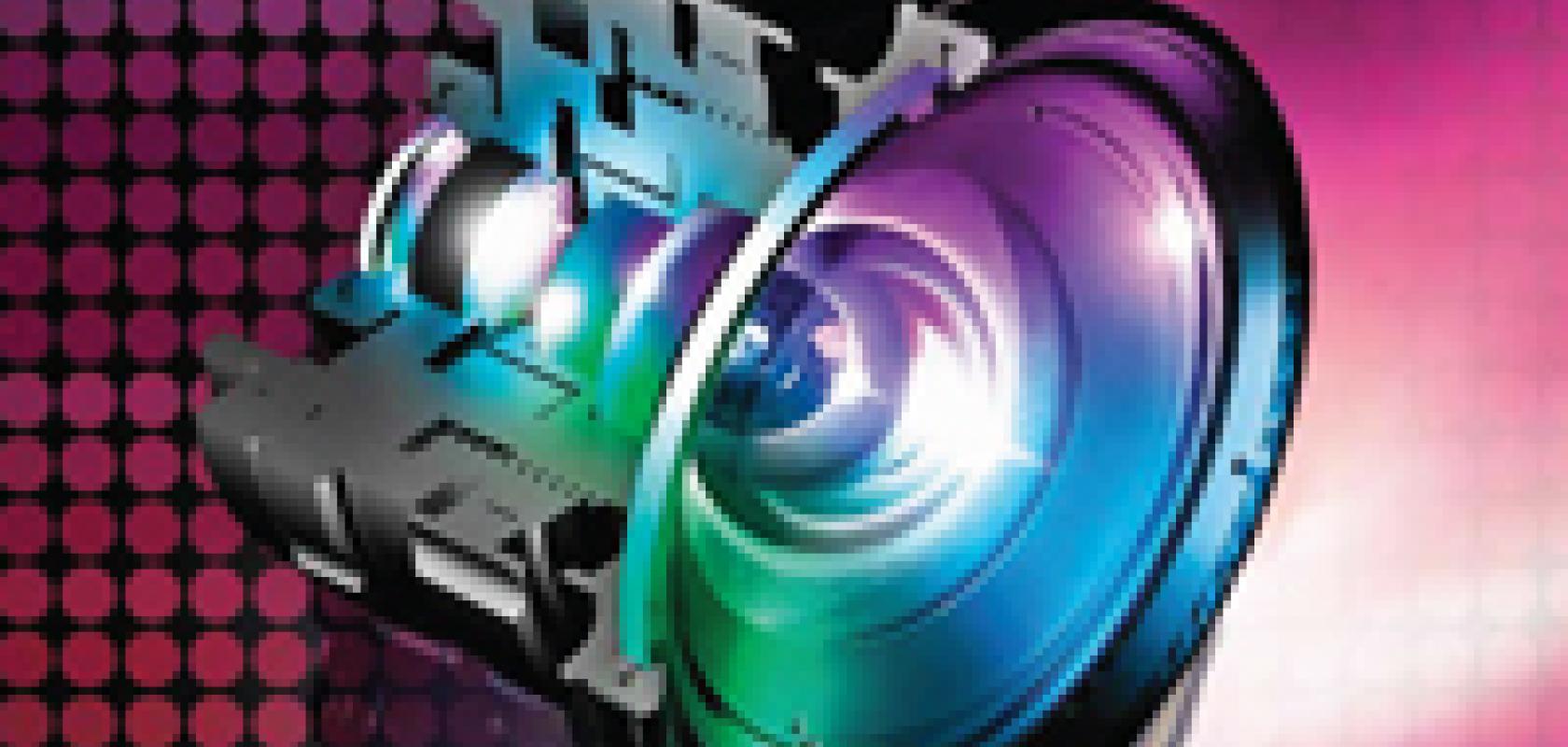
Whether your application is in machine vision, the life sciences, security, or traffic solutions, understanding the fundamentals of imaging technology significantly eases the development and deployment of sophisticated imaging systems. While advancements in sensor and illumination technologies suggest limitless system capabilities, there are physical limitations in the design and manufacture of these technologies. Optical components are not an exception to such limitations, and optics can often be the limiting factor in a system’s performance.
The content provided in this guide is designed to help you specify an imaging system, maximize your system’s performance, and minimize cost. We have compiled a number of best practices for creating sophisticated, cost-effective imaging systems that are applicable for most applications. While the following list is nearly exhaustive and should be considered when designing any imaging system, every application is unique and additional considerations may be required.
EO Best Practice #1
Bigger, in many cases, is better. Allow ample room for the imaging system
Understanding a system’s space requirements before building is especially true for high resolution and high magnification requirements. While recent advancements in consumer camera technology have yielded strong results in a small package, they still do not approach the capabilities required for even intermediate-level industrial imaging systems – partially because of their size limitations. Many applications can require complex light geometries, large diameter and long length lenses, and large cameras, in addition to the cabling and power sources required to operate some of the equipment. Avoid having to make sacrifices to system performance just because the system’s space requirements were not considered. It is often advantageous to specify the vision portion of a system first, as it is typically easier to arrange the electronics and mechanics around the vision portion rather than the other way around. It is also important to remember that the illumination scheme is part of the vision system, and the geometry of the object under inspection can often necessitate the use of a large light source such as a diffuse dome (see EO Best Practice #4).
EO Best Practice #2
Don’t believe your eyes
The human eye and brain work together to form an extremely advanced imaging and analysis system that is capable of filling in information that is not necessarily there. Additionally, humans see and process contrast differently than imaging systems. Software analysis should be used to ensure image quality and performance requirements are met. Images that look good to a human viewer may not be usable with an algorithm.
EO Best Practice #3
Danger! Don’t get to close
Due to the constraints of physics, attempting to look at fields of view that are too large relative to a lens’s working distance places excessive demands on the design of the optical component and can decrease system performance. It is recommended to use a working distance of two to four times the desired field of view to maximize performance while minimizing cost. (See example in Figure 1.1.) Remember EO Best Practice #1 and consider the imaging system’s space requirement before building the system. This practice also applies to the relationship between sensor size and focal length. It is best to have focal length to sensor diagonal ratios of two to four to maximize performance.
If a 100mm field of view is required, it is recommended that the system’s working distance be 200 - 400mm. It may be possible that the system’s performance requirements can be met at WD to FOV ratios approaching or exceeding 1 to 1, however, potentially significant cost and performance tradeoffs may be necessary.
Figure 1.1: Two lens designs, 1a (left) and 1b (right), with the same field of view and very different working distances.
Both lenses in Figure 1a and Figure 1b are imaging the same field of view onto the same sensor, but the lens in 1a has a working distance of half of its field of view, while the lens in 1b has a working distance of 3X its field of view. The light passes through the lens in 1a at extreme angles and the light on the edges of the field of view (magenta/red) have a much longer distance to travel than the light in the center of the field of view (blue). In contrast, the lens in 1b achieves the same field of view at shallower angles with a smaller path length difference. As a result, the lens in 1b features a much less complex lens design and provides superior performance at a lower cost.
EO Best Practice #4
Light up your life. It really does matter
While it can seem like an art form, selecting the appropriate lighting geometry is highly scientific. In order for a lens and sensor to effectively work together, strong contrast must be produced by properly lighting the object. The characteristics of the object under inspection and the nature of any defects must be understood so that the proper illumination geometry is used. Keep in mind that sometimes these lights can be very large (see EO Best Practice #1).
EO Best Practice #5
Color matters
The wavelength (color) selected for the illumination can have an enormous impact on improving or reducing system performance. For instance, in an application using both high quality optics and a top-of-the-line sensor, switching from broadband to monochromatic illumination, or between specific wavelengths, can improve performance by a significant amount. As with EO Best Practice #4, the proper choice of wavelength can make the difference between high contrast and no contrast. Depending on whether the wavelength is correctly chosen or not, the color of illumination can determine the success or failure of a system.
EO Best Practice #6
There can be only one; high resolution and large depths of field struggle to co-exist
Maximizing resolution and depth of field requires the same variable, the lens’s f/#, to move in opposite directions. Essentially, it is impossible to have very high resolution over a large depth of field. Physics dictates that this cannot be done and compromises will need to be made or more elaborate solutions, such as using multiple imaging systems, will need to be employed.
EO Best Practice #7
There is no universal solution; a single lens that can do everything does not exist
As resolution requirements increase, the ability to decrease aberrations (attributes of optical design that adversely affect performance) becomes increasingly difficult over a wide range of working distances and fields of view. Even without budget constraints, there are limitations. For this reason a wide range of lens solutions for similar applications are required.
WANT TO HAVE MORE TIPS?
GET THE COMPLETE SET OF 11 TIPS AND LEARN ABOUT ESSENTIAL FUNDAMENTALS.
GET IN TOUCH WITH US TODAY:
“All Tips for Better Imaging”